The Requirements
To be a good fit for the APQP Quality Engineer opportunity you should have: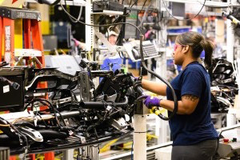
- A four-year degree in Quality Control, Engineering or similar, ASQ Quality Engineer certification, or an equivalent combination of education and experience.
- 3 years in an automotive manufacturing environment as a Quality Engineer or Quality Supervisor; the ideal candidate will have Ford experience.
- 2 years of experience in auditing component supplier PPAP submissions for the automotive industry. Must have an in-depth understanding of the PPAP process. Quick question for you - click here
- 1 year of experience with GD&T studies required.
- The ability to perform and interpret gauge R&R studies.
- Computer proficiency including:
- Minitab, required.
- Proficiency in customer/supplier computer software programs such as IMDS, Ford’s VPP, GM’s CEMENT, GM-GQTS etc.
- MS Office Suite (e.g. Excel, Word, PowerPoint).
- Basic AIAG or related quality system knowledge of ISO 14001 and TS 16949.
- Basic understanding of CMM methods/process.
- Demonstrated competency in metrology, blueprint reading.
- Ability to maintain confidentiality regarding products, services and processes.
- Proven analytical reasoning and problem-solving abilities.
- Excellent interpersonal and communication skills to work with customers, suppliers and peers.
- Ability to work proactively and independently while also serving as a strong team member.
- A valid driver's license.
- Ability to travel to other plants as required (up to 75% at times, though travel ebbs and flows) to support product launches at various stages.
- Multi-site experience.
- Experience with color harmony/appearance processes.
- Experience with APQP / Supplier development.
- Skill with MS Project & Visio.
The Role
Reporting to the Corporate APQP Manager, as APQP Engineer, you will join an outstanding team including two other APQP Engineers, each focused on a specific OEM, a CMM Technician and a Quality Technician. The team is based in our Holt, MI facility, but is often dispersed to other plants depending upon the stage of current launches. You will support several launches, including different products and lines, at various stages simultaneously, traveling to the plant responsible for the launch as needed.We have plants in Holt, Brownstown, Rochester, Lansing and Sterling Heights, MI, Chicago, IL, Louisville, KY, Toledo, OH and Ontario, Canada. While you could travel to any of our plants, you will spend the majority of your travel time in Chicago (most often), Louisville and Brownstown, where we produce and sequence the majority of our Ford products. Travel ebbs and flows but can be extreme at times. Typically, you'll travel around 70%, with 35% being overnight. Hours also flex with workflow. Quick question for you - click here

Your wide breadth of responsibilities will include:
- Establishing quality engineering disciplines during the development phases of products to ensure that quality objectives are met.
- Engineering, documenting, communicating and/or implementing quality deliverables as defined by internal procedures, customer requirements, and industry standards for assigned advanced program commodities.
- Reporting APQP status and issues that may directly or indirectly lead to the detriment of quality or financial performance of the assigned advanced program commodities.
- Working with Suppliers and Customers to communicate quality issues for assigned responsibilities.
- 8-D’s,8-Steps, PPSR’s, 5 Whys, DMN’s, Quality Alerts
- Working on setting up and monitoring program PPAPs submission level for the following:
- Design FMEAs,
- Dimensional Results,
- Measurement system analysis (including Gage R&R reports in Minitab), Quick question for you - click here
,
- Initial process studies (prototype, launch & production),
- Customer specific requirements
- Records of Material and performance test results,
- Design records,
- Engineering change documents,
- Customer engineering approvals,
- PPAP warrant,
- Process flow (prototype, launch & production),
- Process FMEA (prototype, launch & production),
- Control plan (prototype, launch & production),
- Qualified laboratory documentation,
- Appearance approvals (AAR),
- Sample product,
- Master samples,
- Checking aids.
- Reviewing a concurrence of influential engineering inputs to assigned advanced program commodities to verify that expectations of requirements and workmanship are demonstrated.
- Reviewing, dispositioning, and documenting communication of discrepancies for supplier sample submissions of new or changed, advanced program materials.
- Coordinating and preparing required inputs and outputs to ensure that customer product; material and documentation submissions are accurate, timely and complete.
- Documenting all activities as required.
- Adhering to all company guidelines for emergency evacuation to ensure employee safety.
- Advise the department manager of those situations that may pose a significant risk to the program, product assurance, facilities, employee safety or customer satisfaction results.
- Initiate actions to prevent the occurrence of any nonconformance relating to product, process & systems.
- Identify and record any problems relating to the product, process or system.
- Initiate, recommend or provide solutions through the appropriate channels and verify implementation.
- Control further processing and delivery of nonconforming product until the deficiency is corrected.
Note: this description is intended to give you a general overview of the position and is not an exhaustive listing of duties and responsibilities.
Video: the latest robotic loading process at Dakkota Windsor demonstrates the company's commitment to staying on the leading edge.
More Good Reasons
Professional developmentThis is a role where you must come in with deep technical knowledge, but where you'll also enjoy ample opportunities to expand your knowledge.
Career options
While this role could keep you happy and challenged for years to come, once you have proven yourself as APQP Engineer, you will be free to pursue other opportunities within Dakkota, in Holt, other facilities, or on our Corporate team. For example, this role has been a springboard to management on several occasions.
Value-driven company
Dakkota CEO Andra Rush has created companies that do more than generate profit: they impact the local community and economy by providing training and putting Americans to work. Rush was honored by President Obama in his State of the Union address in January 2014, along with GM CEO Mary Barra, for demonstrating the "strength of our work ethic and the scope of our dreams."
Award winning
You will work for a highly respected, award-winning company. Consider a few of our many accolades:
- 2016 Michigan Minority Supplier of the Year (MMSDC)
- 2015 National Minority Supplier of the Year (NMSDC)
- 2015 GM Supplier of the Year
- 2014 Michigan Minority Supplier of the Year (MMSDC)
- 2014 GM Supplier Quality Excellence Award
- 2014 GM Supplier of the Year
- 2013 GM CCA Platinum Shipping Award
- 2013 Ford World Excellence Silver Award - Headliners
- 2013 Ford World Excellence Award - Diverse Supplier of the Year
- 2013 General Motors Supplier of the Year
- 2013 Chrysler Group Supplier of the Year - World Class Manufacturing
- 2013 Chrysler Group Supplier of the Year - Quality
- 2013 Michigan Minority Supplier of the Year (MMSDC)
- 2012 Michigan Minority Supplier of the Year (MMSDC)
- 2012 Chrysler's World Class Manufacturing (wCM) for Suppliers Program
At Dakkota we strive to enhance the communities where we live and work by being environmentally and socially responsible and ensuring fair and equitable employment. We provide multiple opportunities for employees to make a positive impact on their community by devoting volunteer hours and resources to local charities, as you can see in the pictures here. We're always looking for new ways to make a difference. Our employees have supported organizations like the United Way, Salvation Army, and Autism Speaks, as well as local food banks and schools.
Great Environment
We enjoy working together toward common goals here at Dakkota. In fact, we have vision and culture committees to help clarify and communicate those values. We are also strongly committed to diversity and have been awarded the Michigan Minority Supplier Development Console (MMSDC) Supplier of the Year Award for the last three years. We are a close-knit team, and we celebrate with birth announcements, seasonal picnics and parties, employee service awards, and more.
Excellent Compensation
In addition to a competitive salary and discretionary bonus, we offer top-notch benefits. Our benefits include comprehensive and affordable medical, dental, prescription, and vision insurance programs; a 401(k) plan with company match; flexible spending accounts; tuition assistance; in-house training; company-paid employee life insurance and short-term disability insurance; voluntary employee life insurance and long-term disability insurance; voluntary spousal / dependent life insurance; paid holidays; and paid vacations, tuition assistance and more.
Keys to Success
If you are just looking for a job and a paycheck, this probably isn't the role for you. However, if you are looking for a career home in which you can channel your passion and make your mark in a critical position, you are going to thrive here. Your technical knowledge will be essential -- we need a skilled engineer who can make an impact beginning day one -- but you'll also need strong interpersonal and communication skills to really move the needle. You will work with a range of internal and external stakeholders, so your leadership toolbox should include the ability to influence and motivate others to play their part. Customers can be challenging, so you'll also bring a thicker skin to the table.We understand that there will be a learning curve, but we'll also look to you to leverage your experience to hit the ground running. It will be busy from day one, and you'll need to be able to take ownership of your role and establish yourself quickly.
In addition, in order to be an outstanding APQP Quality Engineer, you will:
- Bring a strong sense of urgency to our fast-paced, high volume environment.
- Develop good working relationships and earn the trust and respect of your co-workers and other stakeholders. You'll know you're hitting the mark when they approach you as the SME.
- Remain flexible and adaptable as priorities change.
- Continuously build your knowledge base.
- Bring a strong sense of ownership and accountability.
- Keep a constant eye out for opportunities to improve processes.
About Us
Dakkota Integrated Systems was formed in 2001 to create a minority contract supplier that could thrive in a fast-paced, cost-competitive environment to support automotive original equipment manufacturers. We have excelled at delivering quality, process control and innovative solutions for warranty and sustainability concerns to address our customers’ needs.Outstanding customer service and agility have propelled Dakkota from one facility with one customer to 13 facilities with GM, Ford, Chrysler, and many other customers in 13 years, earning launch and supplier partner awards along the way. Dakkota was among the first automotive suppliers to be awarded complete interior integration programs for General Motors. We dedicate resources to each new program and co-locate with our customers for a fully integrated approach.
Our in-house capabilities include:
- Extensive use of proven engineering disciplines: DFMEA, GD&T, FEA, VE/VA, and PFMEA
- Development of assembly tooling and fixtures
- Packaging development and validation for complete systems, including customer-directed components
Our vision and culture are firmly based on our high regard for our customers and solid respect for our employees. Dakkota strives to be considered to be one of the best places to work in North America, to maintain our reputation for best-in-class customer service, and to be known as a company that is "built to last."
Video: the May 2017 edition of Driving Dakkota, our video blog, provides an overview of our company's current activities including Business Updates, Great Ideas and Community Service.